12/06/2007 - Practise kits
have arrived
I
ordered a toolbox and control surface practise kit. They
look like this.
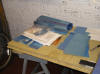
13/06/2007 - A little training
is required
I
needed a few more tools so while I was there I had a little
training on how to rivet. here is a section of a control
surface that has been back riveted. I have finally put
a rivet in!
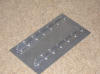
23/06/2007 -
Toolbox started
[2.5hrs]
Cut vinyl strips where edges will meet; smoothed
all the edges of the parts; match drilled the holes for the end
plates; then dimpled the holes for the end plates using the DRDT-2
and also the pneumatic squeezer. Finished by shooting 15
rivets to fit the left hand end plate of the tool box.
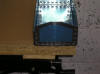
24/06/2007
- Right hand end plate
[1.0hr]
Riveted using the squeezer mainly this time, and
bucked the ones at the bottom and towards the middle where the
squeezer could not get to. Another fifteen rivets done and
to me they look a bit better than on the right hand panel.
Once the plate was on I clecoed the stiffener to the front of the
toolbox.
30/06/2007 - Hinge, Lid, catch,
handle and stiffener
[4.0hrs]
The first today is to fix the hinge to the main
body and lid. The main body comes first; and you will notice
from the first picture below that I drilled the first hole with
the wrong size drill (hence the different colour cleco)
*&^%££%^£^&^. The rivets for the hinge on the main body were
squeezed together using the pneumatic squeezer.
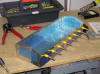
The next mistake I made was to set the hinge to low
on the body (though I did follow the instructions) which meant the
hinge would not close correctly. I decided to reverse the
hinge on the lid. Messy but functional at least. If
this was the empennage I would have had to do it again with new
parts !! Next comes riveting with universal rather than
flush rivets....oh dear, third mistake, damage to skin where I
slipped off and a huge smiley. Heh live and learn and all
that...
The all that was required was the latch, and
handle. The handle has to be bent from wire to make the
shape according to the plans. The first bend I was not happy
with and changed the jig, but had not thought ahead that the
radius on the first bend would be different to all the others.
Now on the plus side, I know all the mistakes, I know what I would
do differently, I have another practise kit to have a go at, this
is only a dress rehearsal and the toolbox does actually work.
Sigh.
I will take it to show my inspector next and he can
wince as much as I have !
05/07/2007
- Inspection ! [Total Hours To Make 7.5hrs]
I am chuffed, I got a general thumbs up for my
first go. Obviously I do need to reduce the number of
mistakes ;-)
07/07/2007
- Control Surface Kit Start
[5.0hrs]
This kit starts out with cutting the
shapes for the stiffeners; 4 in total from aluminium angle.
I kept fitting them to the clecoed structure to make sure I cut
sufficient off using snips so that the skins would lie flat and
not bulge in places. Match drilled the holes for the
stiffeners with the skins and then dimpled the skins and
stiffeners ready for riveting.
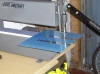
Next job was to back rivet the stiffeners to the
skins. I had to modify my back rivet tool so that I could
set the rivet correctly. Basically the bend in the stiffener
gets in the way and so makes it difficult to get a good
manufactured head, anyway a bit of cutting and grinding later and
the tool is modified. A bit of a shame really, hope it holds
up and does not break :-(
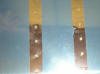
08/07/2007
- Creating the skeleton
[2.0hrs]
Decided to use the squeezer for the
universal rivets this time. Quite pleased with the results,
not marking of heads or of the ribs or spar so quite chuffed.
However the kit calls for using the same length of rivet used to
put the stiffeners on the spar (2nd picture) for attaching the
ribs to the spar. I thought to myself they wont be long
enough, but stuck to the plans. Sure enough it needs a 3.5
shank really. Anyway the 3rd picture shows how little is
left on the manufactured head after binding together the spar,
stiffener and the rib. Next time a longer rivet would be
used !
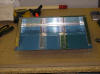
12/07/2007 - Create Jig & match
drill skins
[1.0hr]
Created the jig to hold the assembly as
per the plans (you can see it in the picture for the 13/7.
Debburred all the skins, and ribs and then match drilled all the
holes. The spar does not have any holes in it, but straight
forward anyway.
13/07/2007 - Finish drilling of
skins including trailing edge
[2.5hrs]
The trailing edge has to be drilled at
84 degrees so a little guide
made out of hardboard was made at the correct angle and then the
trailing edge with stiffener was match drilled all the way along.
Started the dimpling process of skins using the DRDT-2.
14/07/2007 - Dimpling
[1.5hrs]
Skins, and the majority of the ribs were
dimpled yesterday, but the
ones near the tips of the ribs are far to tight for squeezer or
for the DRDT-2. The plans call for making a bucking/dimpling
plate thin enough with a hole and countersink in it .... then use
a rivet to make the dimple. I made the plate ok, see
picture below; a bit 'Heath Robinson' but it seems ok. Then
I struggled for 45mins trying to get the rivet to make the right
dimple. I gave up, and took the male die from the DRDT-2,
made a wooden block to protect it when it was hit and belted it
with hammer. The result was much better :-)
Dimpling the spar was none to easy either. I had gone to a
lot of trouble to make the flanges on the spar straight and level
with the skin so the trailing edge remains flat. The
squeezer put paid to that !!! I stopped after the first
dimple as it was straightening the flange. So I used the
dimple pop rivet method to give small dimples and the hand
countersunk the holes. Still not happy with the result so
this will need further work.
15/07/2007 - Trailing edge
stiffener
[1.0hr]
The stiffener must be countersunk using
the micro stop tool and a #40 countersink bit. Whilst the
drilling was done at 84 degrees, the skins were dimpled at right
angles (cant do it any other way....I think?!?)
so the countersink will need to be
at right angles as well to make them all fit together and closely.
My first try makes the leading edge look like a bandy-legged Irish
pit pony. Some tweaking is required to get both sets of skin
dimples to sit nicely in the counterparts of the trailing edge.
Ok a lot of tweaking ! The pictures show how some of the
dimples sit well and others don't causing gaps to appear along the
edge.
17/07/2007 - Riveting the spar [1.5hr]
I did'nt find this bit to easy using the
rivet gun and bucking bar. For the life of me I could not
get the manufactured heads straight and level. Ended up
drilling 4 rivets out (which went well) on the first skin.
Still not happy with the finish but I have decided to move on for
the time being. The second skin although I had to squeeze my
hand inside the rudder section it went surprisingly well ... who
would of though it as I had to blind buck, I could not see a
thing!
18/07/2007 - Riveting the Ribs [2.0hr]
Squeezed most of the flush rivets until
it got too tight, so decided as per plans to use a self made
bucking bar with the rivet gun and mushroom set. Disaster,
the gun slipped and I dented the skin. *^&$*^$*&%^(*^)(*^&(*)&^*(.
The mushroom set I have is a small set with no rubber guard, so I
have ordered a rubber swivel mushroom set instead. I also
could not finish off the last rivets in the rib close to the
trailing edge, and trying to buck them was unsatisfactory.
Time to order a 'no hole' yolk for the pneumatic squeezer!!
I can not continue now until the 'no hole' yolk
arrives. Once the final riveting is done on the ribs, I can
get on the with the trailing edge double flush rivets and bending
the leading edge. 16.5 hours so far. Next update will
be about 26th July.
04/08/2007 -
Trailing Edge & Leading Edge [2.0hr]
Some more tools finally turned up a 'no
hole yoke' and a rubber guarded mushroom set which I hope will
stop me putting dents in the skin ! Anyway first job was
using the no hole yoke to set the final rivets in the rib.
Then my attention turned to the leading edge and double flush
rivets. They were ok actually just follow the instructions
and hey presto...well ok maybe not there is a slight bend but it
less than 0.1". Then it was bending the leading edge which
took a bit of perseverance but got there in the end.
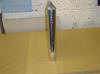
With it all done it was a quick trip to see my
inspector who was generally ok for me to continue. He made
two comments other than "its a bit small isn't it"; the first was
try not to dent the skin, and the other was the training edge
needs to be straighter. Bob I need another jig !!!!!!
Anyway it earned me a signature in my PFA log book
and I can make a start for real.